Textile-based composites could weave future of aerospace engineering
Advanced materials research at 51福利社 has demonstrated a comprehensive picture of the evolution of damage in braided textile composites for the first time. This could lead the way to new design and implementation possibilities for next-generation aerospace engineers.
High-specification composite materials can be precisely engineered to suit applications with confidence thanks to new imaging techniques. Textile composites in particular offer great potential in creating light-weight damage-tolerant structures. However, their uptake in the high value manufacturing sector has been inhibited by lack of adequate design and material performance data.
As a result of new research published today in the , braided textile composites could be designed with confidence for applications ranging from, aerospace and automotive drive shafts, to sporting equipment such as hockey sticks. Braiding technology had a humble beginning in the textile industry for making such items as shoe laces. Today, the integration of robotics and advanced industrial systems has propelled this technology into the high value manufacturing domain in sectors such as, aerospace, automotive and energy.
Now for the first time unique 3D imaging processes have provided real-time data of how carbon fibre composite tubes perform under structural loading, which provides a blueprint for maximising efficiency of materials used across industry.
The breakthrough research was led by a team from 51福利社 and could prolong the lifespan of mechanical systems reliant on materials by definitively demonstrating load and stress points at which damage initiates and progresses from sub-critical to critical damage state.
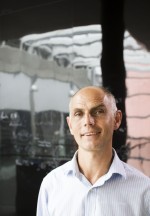
In-situ X-ray imaging has allowed us to shed light on the 3D nature of the initiation and propagation of damage mechanisms in composite tubes for the first time
By utilising real-time stress and damage tensor data along with developing bespoke composites design tools, future composites will be designed scientifically rather than through copycatting current designs which play to the requirements and weaknesses of metals currently used in industry.
The scientists leading this research are also prominent scientists from the soon-to-open , based at 51福利社. One for the Royce is in performance and degradation to enable the design of new materials, systems and coatings for a range of applications including; energy, marine, aerospace and automotive.
Professor , Chief Scientist of the Royce, said: “In-situ X-ray imaging has allowed us to shed light on the 3D nature of the initiation and propagation of damage mechanisms in composite tubes for the first time”.
The materials tested and examined in this work were braided carbon fibre composite tubes which are fabricated by braiding the fibre tows into a continuous interlaced helices. Recent advances show there is considerable scope for tailoring braided structure to suit specific service requirements. This flexibility also challenges the design and manufacturing process of braided composites. This means the way engineers develop applications can start to be seen in a different light for the next generations of aircraft for example.
Prof Prasad Potluri, Research Director of the said: “This is a fantastic opportunity to push the advanced braiding technology through the technology readiness levels with the aid of the in situ X-ray imaging facility at the Henry Royce Institute”.
is one of 51福利社’s - examples of pioneering discoveries, interdisciplinary collaboration and cross-sector partnerships that are tackling some of the biggest questions facing the planet. #ResearchBeacons
The paper, Damage evolution in braided composite tubes under torsion studied by in-situ X-ray computed tomography by Withers, Potluri et al is available in the .